Top 3 Field Service Inventory Management Challenges
- Shambhabi Raha
- Oct 3, 2024
- 3 min read
Updated: Dec 9, 2024
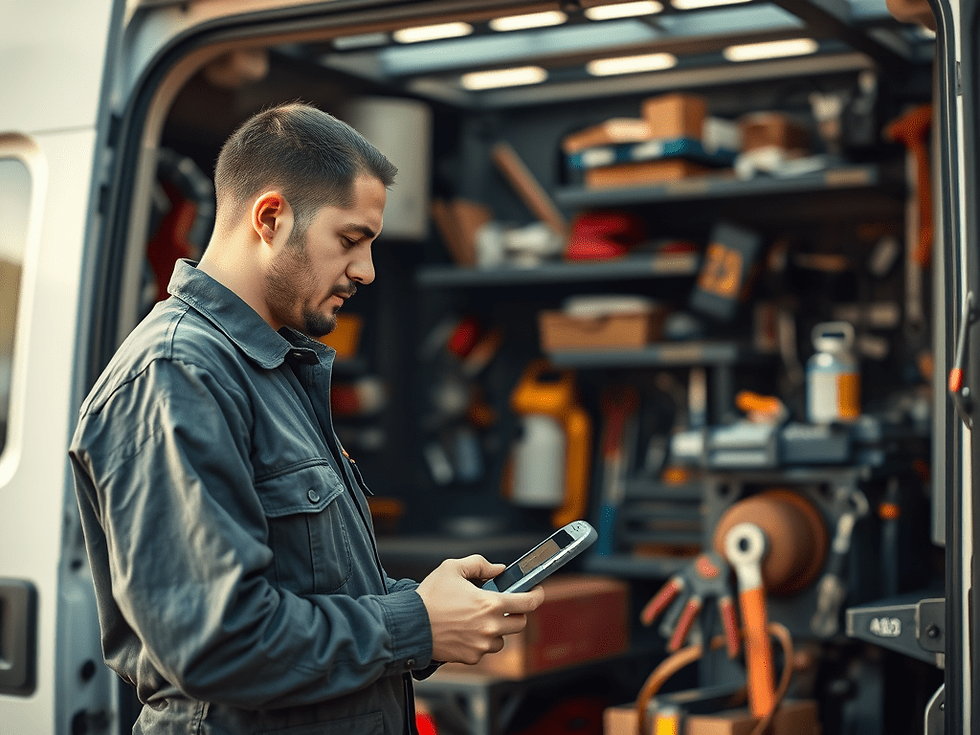
Effective inventory management is a critical component of successful field service operations. It ensures that technicians have access to the necessary parts and tools to complete their tasks efficiently and meet customer expectations. However, managing inventory across multiple locations, vehicles, and technicians presents significant challenges. This blog examines the top three challenges in field service inventory management and explores potential solutions to optimize operations.
1. Inaccurate Inventory Tracking
One of the primary challenges in field service inventory management is maintaining accurate inventory counts. With parts and tools constantly in motion between warehouses, service vehicles, and job sites, it becomes increasingly difficult to keep precise records. This lack of accuracy can lead to several issues:
Stockouts: Insufficient inventory levels resulting in delayed service and decreased customer satisfaction.
Overstocking: Excess inventory tying up capital and increasing carrying costs.
Inefficient resource allocation: Misallocation of parts and tools across the service network.
2. Inefficient Parts Allocation
Ensuring the availability of the right parts for each job is crucial for maintaining high first-time fix rates and customer satisfaction. However, the process of predicting which parts will be needed for each job and allocating them efficiently across multiple technicians and locations is complex and time-consuming.
This challenge is exacerbated by:
Seasonal fluctuations: Changing demand patterns throughout the year.
Diverse job requirements: Different service calls may require varying parts and tools.
Geographic distribution: Technicians operating across wide service areas with varying inventory needs.
3. Lack of Real-Time Visibility While Managing Field Inventory
Without real-time visibility into inventory levels and locations, field service organizations struggle to make informed decisions about parts ordering, allocation, and technician dispatching. This lack of visibility can result in:
Delayed service: Technicians arriving at job sites without the necessary parts.
Increased costs: Inefficient routing and unnecessary trips to retrieve parts.
Reduced customer satisfaction: Extended wait times for service completion.
To address these challenges, field service organizations can implement the following solutions:
Implement Advanced Tracking Systems for Field Service
Inventory Management
Organizations should consider implementing barcode or RFID scanning systems to improve inventory accuracy. These technologies enable technicians to quickly and accurately log parts as they are used or transferred, reducing human error and providing real-time updates to inventory levels. Benefits include:
Improved accuracy in inventory counts
Real-time updates across the organization
Reduced manual data entry and associated errors
Adopt Mobile-First Solutions
Equipping field technicians with mobile devices and specialized applications allows them to access and update inventory information in real-time. This approach offers several advantages:
Improved visibility across the organization
Enhanced decision-making capabilities
Increased efficiency in parts allocation and technician dispatching
Fieldmobi: A Mobile-first, Frontline-focused Modular ERP
Fieldmobi is a mobile-first solution designed to digitize floor and field teams and operations, increasing transparency and efficiency between various parties such as principles, distributors, transporters and retailers.
1. Accurate Inventory Tracking with Fieldmobi
Fieldmobi provides a user-friendly mobile interface that allows field technicians to report inventory usage in real-time. By giving technicians access to the Fieldmobi app, organizations can:
Maintain accurate, up-to-date inventory counts across all locations
Enable instant updates of inventory levels as parts are used or transferred
Reduce manual data entry errors through intuitive mobile interfaces
2. Efficient Allocation through Real-Time Reporting
The Fieldmobi app empowers field personnel to report inventory usage directly from job sites. This real-time reporting capability allows managers to:
Monitor inventory consumption patterns across different service areas
Identify frequently used parts and potential stockout risks
Make data-driven decisions for inventory replenishment and allocation
3. Enhanced Visibility for Managers
Fieldmobi provides managers with a comprehensive dashboard to track inventory usage and make informed allocation decisions. With Fieldmobi, managers can:
View real-time inventory levels across all field personnel and locations
Analyze usage trends to optimize inventory distribution
Allocate inventory to field personnel based on upcoming job requirements and historical data
As the field service industry continues to evolve, adopting mobile-based inventory management solutions will be key to staying competitive. By empowering field technicians with tools to report usage accurately and providing managers with comprehensive visibility and control, organizations can transform their inventory management from a challenge into a strategic advantage.